SHS series socket welder | TPWC series Band saw |
TPW series manual butt fusion machine | TPWG series workshop welding machine |
TPWY series butt fusion machine | Series special tools |
QZD series Auto-butt fusion machine | SHM series saddle fusion machine |
Type | TPWG315 | |
Materials for welding | PE,PP ,PVDF | |
Outside Diameter ranges | elbow (DN,mm) | 90 110 125 140 160 180 200 225 250 280 315mm |
tee (DN,mm) | 90 110 125 140 160 180 200 225 250 280 315mm | |
cross (DN,mm) | 90 110 125 140 160 180 200 225 250 280 315mm | |
Wyes 45°& 60° (DN,mm) | 90 110 125 140 160 180 200 225 250 280 315mm | |
Environment temperature | -5~45℃ | |
Hydraulic oil | 40~50(kinematic viscosity)mm2/s, 40℃) | |
Power supply | ~380 V±10 % | |
Frequency | 50 Hz | |
Total current | 13 A | |
Total power | 7.4 KW | |
Include, heating plate | 5.15 KW | |
Planing tool motor | 1.5 KW | |
Hydraulic unit motor | 0.75 KW | |
Insulating resistance | >1MΩ | |
Max. hydraulic pressure | 6 MPa | |
Total section of cylinders | 12.56 cm2 | |
Max. temperature of heating plate | 270℃ | |
Difference in surface temperature of heating plate | ± 7℃ | |
Undesired sound | <70 dB | |
Oil tank Volume | 55L | |
Total weight(kg) | 995 |
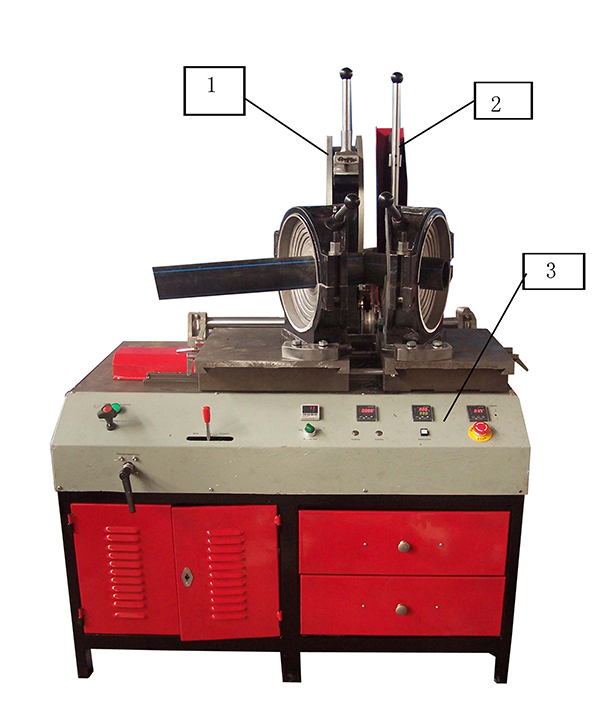
1. Planning tool | 2. Heating plate | 3. Operation panel |

1. Pressure Regulation Valve | 2. Pressure Relief Valve | 3. Oil Pump Working Indicator | 4. Direction Valve |
5. Digital Pressure Meter | 6. Planing Button | 7. Timer | 8. Soaking Time Button |
9. Temperature Control Meter | 10. Cooling Time Button | 11. Voltmeter | 12. Heating Switch |
13. Emergency Stop | 14. Buzzer |
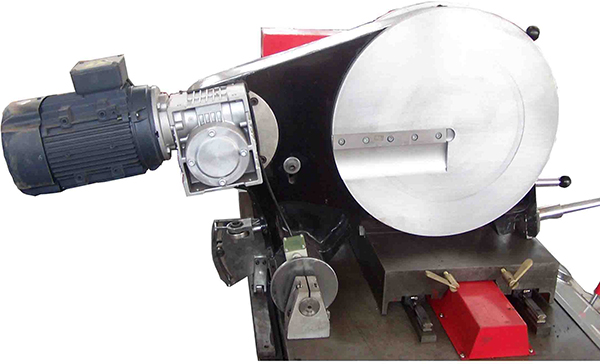

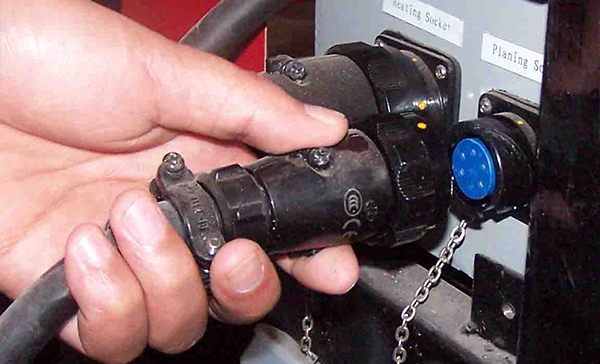
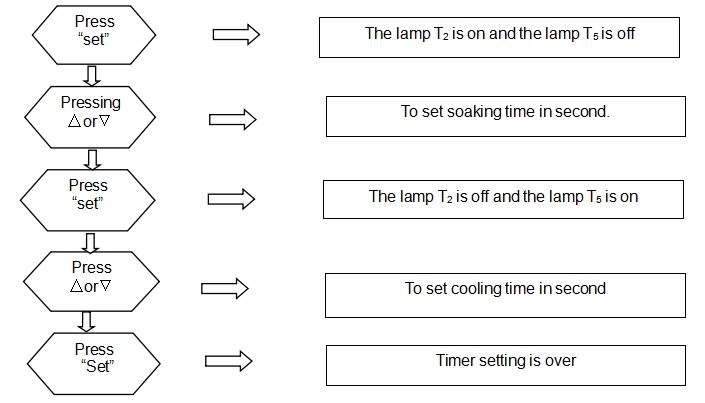
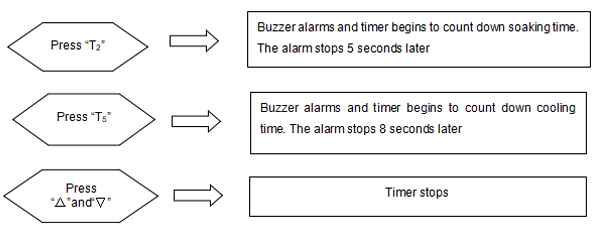
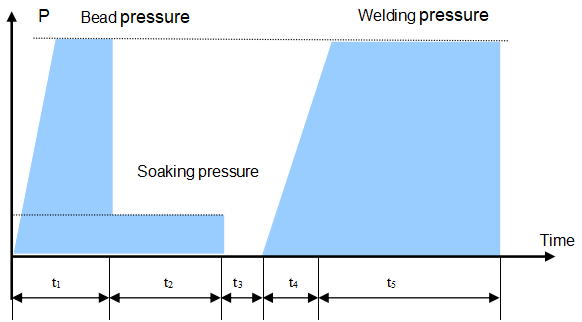
Wall thickness (mm) | Bead height(mm) | Bead build-up pressure(MPa) | Soaking time t2(Sec) | Soaking pressure (MPa) | Change-over time t3(sec) | Pressure build -up time t4(sec) | Welding pressure(MPa) | Cooling time t5(min) |
0~4.5 | 0.5 | 0.15 | 45 | ≤0.02 | 5 | 5 | 0.15±0.01 | 6 |
4.5~7 | 1.0 | 0.15 | 45~70 | ≤0.02 | 5~6 | 5~6 | 0.15±0.01 | 6~10 |
7~12 | 1.5 | 0.15 | 70~120 | ≤0.02 | 6~8 | 6~8 | 0.15±0.01 | 10~16 |
12~19 | 2.0 | 0.15 | 120~190 | ≤0.02 | 8~10 | 8~11 | 0.15±0.01 | 16~24 |
19~26 | 2.5 | 0.15 | 190~260 | ≤0.02 | 10~12 | 11~14 | 0.15±0.01 | 24~32 |
26~37 | 3.0 | 0.15 | 260~370 | ≤0.02 | 12~16 | 14~19 | 0.15±0.01 | 32~45 |
37~50 | 3.5 | 0.15 | 370~500 | ≤0.02 | 16~20 | 19~25 | 0.15±0.01 | 45~60 |
50~70 | 4.0 | 0.15 | 500~700 | ≤0.02 | 20~25 | 25~35 | 0.15±0.01 | 60~80 |

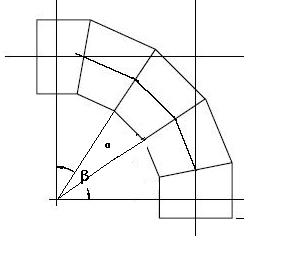
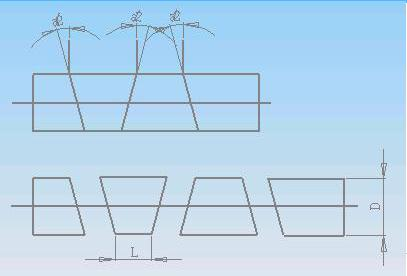
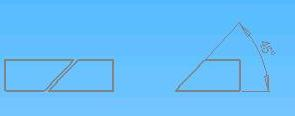
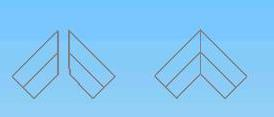
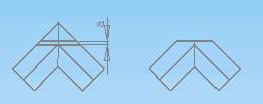
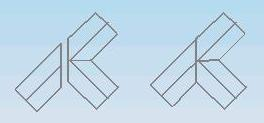
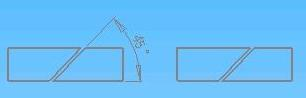
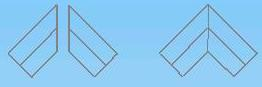
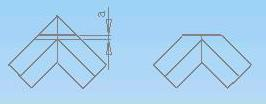
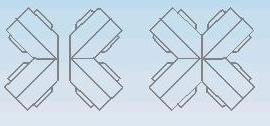


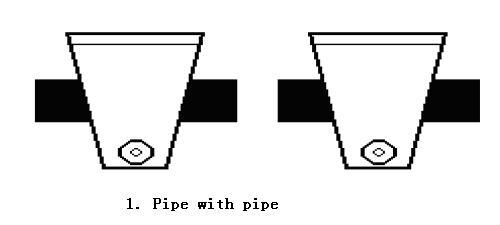

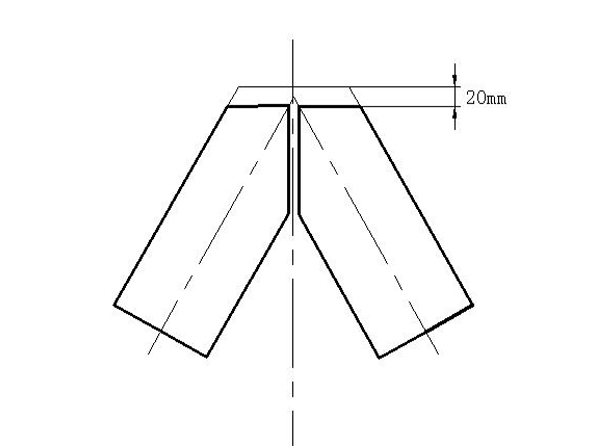
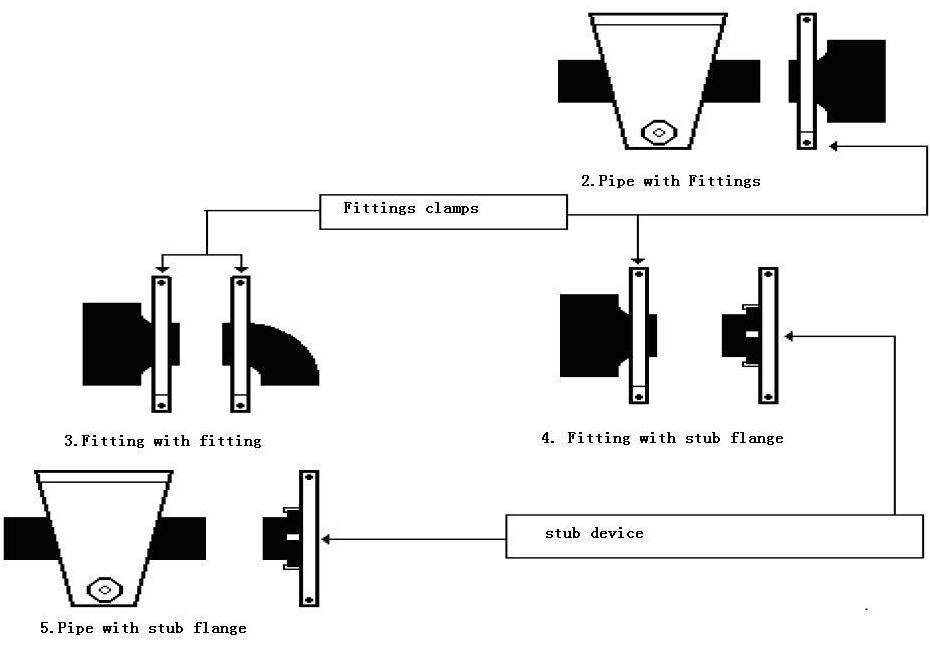
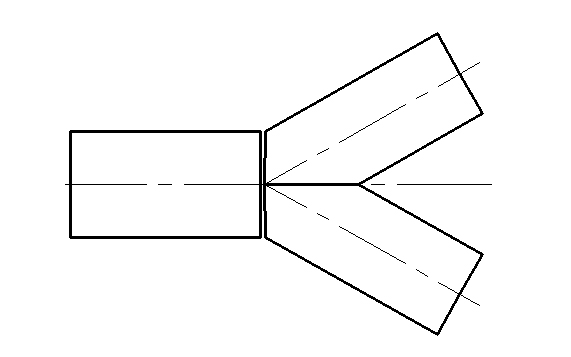
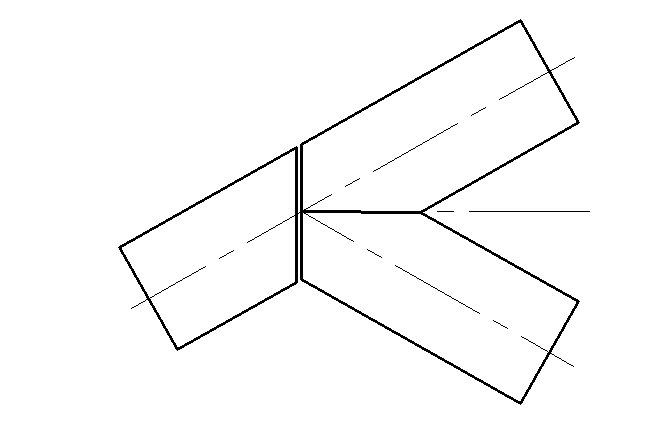
Malfunctions of hydraulic unit | |||||
No | malfunction | analyzes | solutions | ||
1 | The motor does not work |
| |||
2 | The motor rotate too slowly with abnormality noise |
| than 3 MPa
| ||
3 | The cylinder works abnormally |
| to outgo the air. | ||
4 | Dragging plate moving cylinder does not work |
|
| ||
5 | Cylinder leak | 1. The oil ring is fault2. The cylinder or piston isdamaged badly | 1. Replace the oil ring2. Replace the cylinder | ||
6 | The pressure can not be increased or the fluctuation is too big | 1. The core of overflow valve is blocked.2. The pump is leak.3. The joint slack of pump isloosened or key groove is skid. | 1. Clean or replace the coreof over-flow valve2. Replace the oil pump3. Replace the joint slack | ||
7 | Cutting pressure can not be adjusted | 1. The circuit is fault2. Electromagnetic coil is fault3. The overflow valve is blocked4. Cutting overflow valve is abnormal | 1. Check the circuit (the red diodein the electromagnetic coil shines)2. Replace the electromagnetic coil3. Clean the core of over-flow valve4. Check the cutting over-flow valve | ||
Malfunctions of electrical units | |||||
8 | The whole machine does not work |
| 1. Check the power cable2. Check the working power3. Open the ground fault interrupter | ||
9 | Ground fault switch trips |
| 1. Check the power cables2. Check the electrical elements.3. Check the higher-up powersafety device | ||
10 | Abnormally temperature increasing |
| contactors
| ||
11 | Lose of control when heating | The red light is shine, but the temperature still goes up, that is because the connector is fault or the joints 7 and 8 can not open when get the required temperature. | Replace the temperature controller | ||
12 | Planing tool does not rotate | The limit switch is ineffective or the mechanical parts of planing tool are clipped. | Replace the planning tool limit switch or minor sprocket |
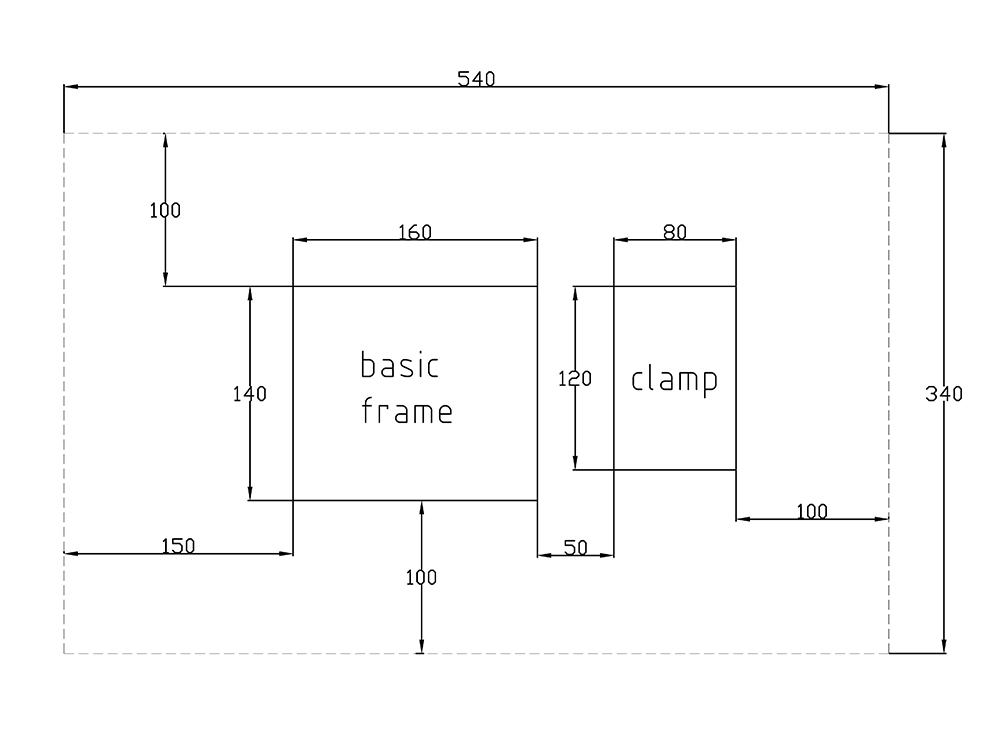